It’s hard to imagine our daily life without a refrigerator. Like any equipment, the refrigerator has an electronic filling, which is responsible for the operability of the equipment. The main element is the compressor. This part is responsible for the production of frosty air. This is the meaning of the detail. If at some point you find a malfunction in refrigerator operation, you should check the compressor for serviceability.
The causes of the problems can be different. In this article, we will talk about how to fix the compressor and set up the equipment yourself, without the help of masters and without contacting the service center. How to check performance refrigerator compressor it is important to understand.
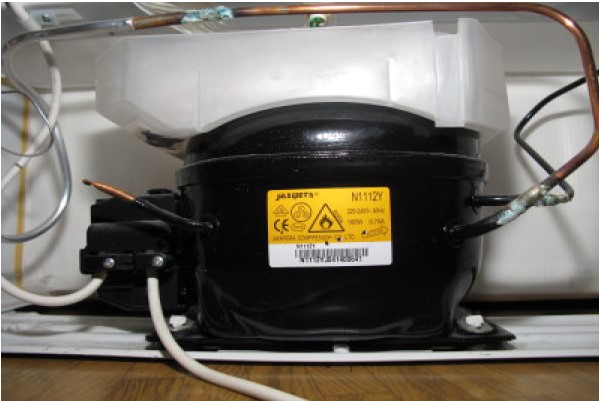
Refrigerator compressor
Basic principles of the motor
The principle of operation of most refrigerators is the same. In models such as Indesit, Beco, Atlant, cooling systems work by circulating freon, which is responsible for cooling. So gas, using a compressor under high pressure, enters the condenser, where there is cooling, liquefaction and vaporization of gas, then the reverse process occurs. A similar scheme is inherent in all refrigerators with built-in No Frost system. In older models, evaporation products deposited on the wall turn into ice.
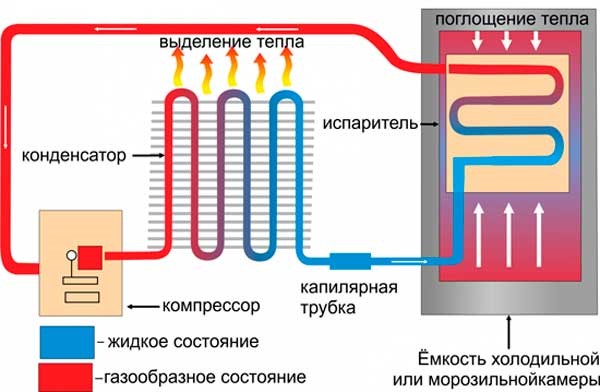
The scheme of the motor
The temperature inside the refrigerator compartment is controlled by the thermostat. The cooling level can be set by the user. When the mode is set, the signal enters the motor starting relay, which is responsible for the operation of the mechanism. The compressor itself is located on the rear side of the structure and is protected by a casing from the harmful effects of liquid particles.
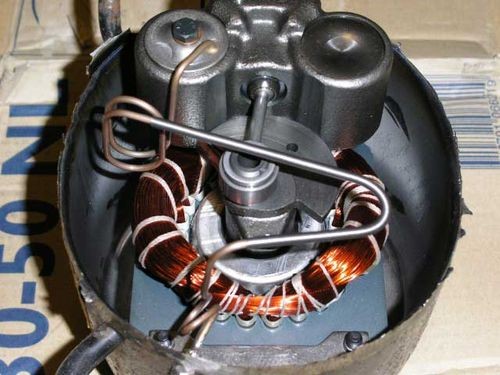
Compressor location
The housing is connected by one main and two accessory leads. The main one connects all the mechanisms with each other and is responsible for the even distribution of energy. Two clauses serve as conductors of electric current to the starting mechanism. Most modern refrigerator models are equipped with a convenient wiring diagram.
How to check the compressor for performance
The compressor is called “the heart of the refrigerator” for a reason. If he stops working, this can be reported either by the absence of frosty air, or complete silence. There are three possible causes of failure:
- The electronic filling of the compressor burned out. Most often, this happens during sudden changes in voltage: during a severe thunderstorm, or during a short circuit
- The protective mechanism of the start relay is in a malfunctioning state
- Wiring fault
If you suspect that the compressor is defective, an independent check can confirm. First you need a multimeter, a special device for measuring the frequency of oscillations of electric waves. Once you get to the motor, attach the probes to each of the contacts. If the display shows an infinity sign, then the compressor is in perfect order. If after touching the device shows a certain number, then one of the windings is defective. If all the contacts are OK, but the motor does not work at full power, you can do it yourself. In the next section, we will examine in detail how to check the compressor in the refrigerator.
Diagnostic Methods
For a detailed study, you will need to inspect the compressor from the inside. Here, the value of the numbers displayed on the display of the multimeter may have a different value.For diagnostics, you will need to remove the protective cover and get to the compressor filling. To do this, you need to follow these steps:
- Disconnect wires from motor contacts
- Have a bite of connecting tubes
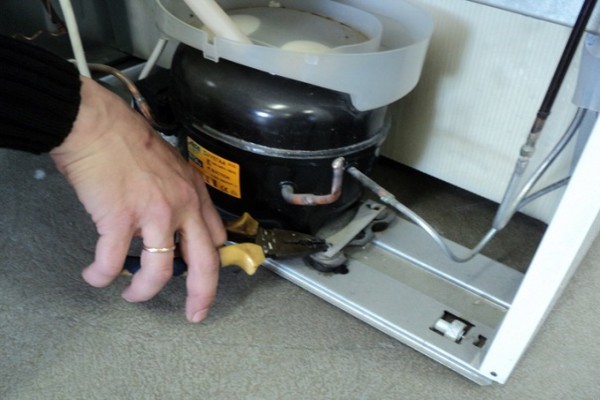
Compressor disassembly process
- Remove the bolts securing the cover
- Remove the screws holding the relay
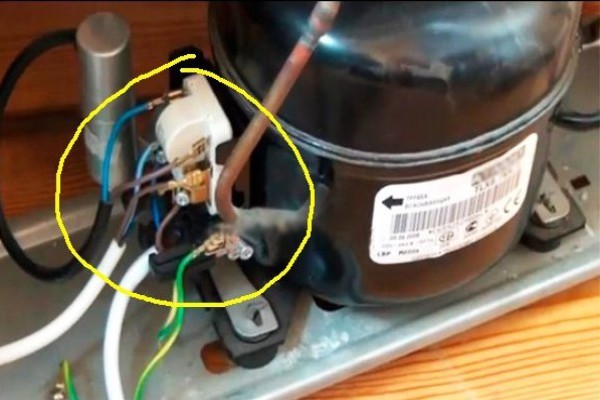
Dismantling the relay
- Next, prepare a multimeter and check the resistance level between the contacts
- Check the performance of the left output pin
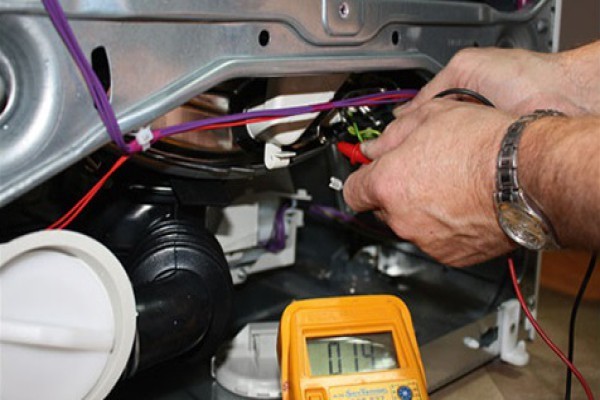
Resistance measurement
Important! The optimal resistance level is about 30 ohms. The top right pin should have a value of 15 ohms. For the upper left norm, a resistance of 20 ohms is considered.
Here, a certain error of five units is permissible. It all depends on the model of the refrigerator used and how the multimeter rings. Check the manual for possible statistical errors.
If the indicators do not meet the agreed norm, then the motor should be repaired by soldering broken wires, or replaced if the compressor itself cannot be repaired.
Pressure measurement
If all indicators are within normal limits, but the equipment continues to fail, you will need to use a manometer to measure the level of wave oscillations.
- Attach a suitable hose to the injection shooter
- Activate the mechanism
- Record pressure indicators
Pressure measurement
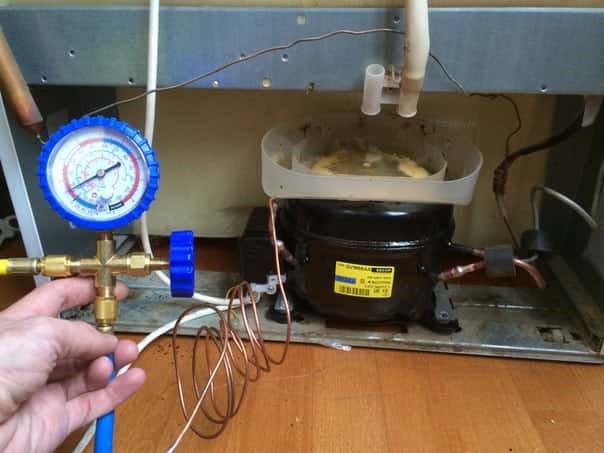
Pressure measurement
The optimal performance for a large two-chamber refrigerator is 6 atmospheres. For medium or small - 4-5 atmospheres. You will need to quickly disconnect the pressure gauge so that it does not break.
Rules for connecting the engine through a cord
If you performed a check on all indicators, but the unit still does not work, you just have to check the motor without starting the relay by performing a direct connection. Strictly follow the diagram so as not to disrupt the operation of the device.
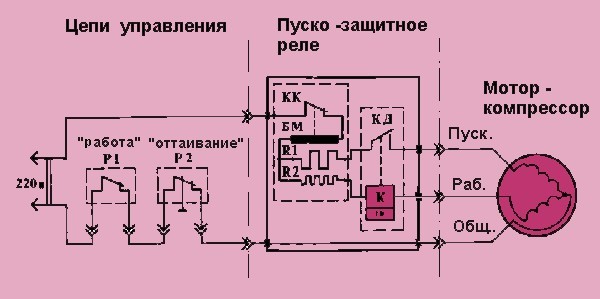
Motor Power Scheme
Using a measuring device, check the current power in the mains lead that leads directly to the compressor. If the power is 140 watts, then the optimal performance is 1.3 amperes. With a power of 120 watts - 1.1 or 1.2 amperes. In the same way, you can check the contacts of the start relay.
It is important to remember that such checks carry a risk to human life. Before you start testing the compressor, thoroughly dry your hands and wrap electrical tape around your fingers. Electrical wiring requires a competent approach, so you better trust a professional craftsman.